サービス
特殊ブロー金型による部品一体化提案
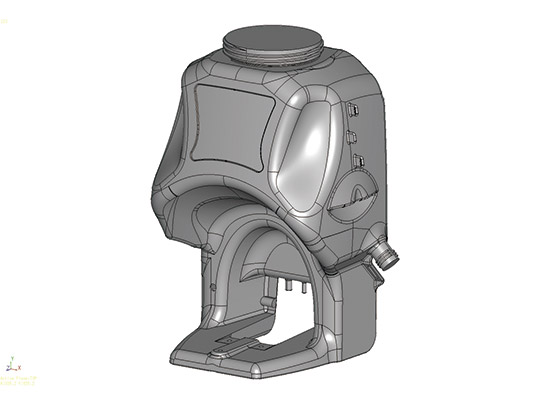
ナットや射出成形品をインサートするブロー成形金型や、板形状とタンク形状を一体成形できるようにしたり、強度や精度を向上させるための分割面の最適化など、特殊なダイレクトブロー成形用の金型の設計については、数多くの事例がございます。
Feature
特殊ブロー金型による部品一体化提案の
3つの特徴
01
インサート付きダイレクトブロー成形を実現する金型設計
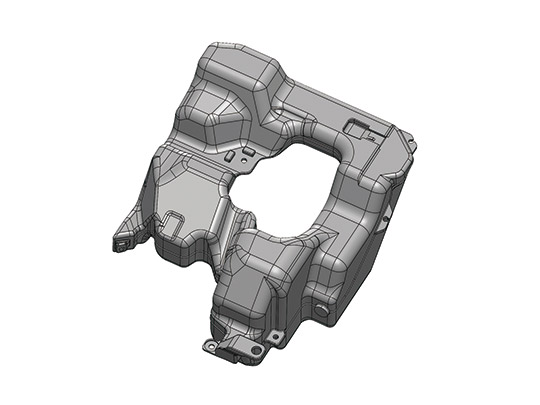
当社が得意とする特殊ブロー金型は、インサート部品を事前にセットすることができるため、ブロー成形後の溶着工程がなくなり、部品の一体化を実現することができます。
しかし、そのためには、アンダー形状を考慮して割り型にすべきか、インサート部品の配置を前提として、スライド同士が干渉しないようにどの位置にスライドを設けるか、といった様々な観点で最適な金型設計をする必要があります。
当社では、インサート付きダイレクトブロー成形用金型の設計・製造実績が多数ございますので、ブロー成形における部品点数削減のご提案を積極的にいたします。
02
射出ダイレクトブロー成形品向けの金型製作実績
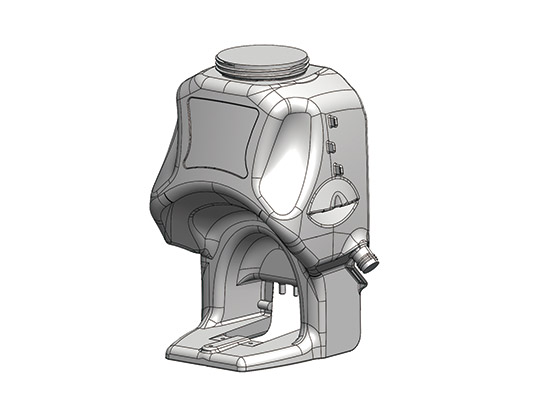
ダクトやウォッシャータンク、薬剤タンク等のブロー成形金型の設計から製作についても、様々なお客様よりご相談をいただいております。
これらのタンク形状の場合は、ブロー成形が最適となりますが、一部は射出成形の方が形状的に適しています。
しかし、射出成形品とブロー成形品の溶着工程が発生してしまうからなんとかしたい、というケースも一部存在します。
当社では、そのような射出成形とブロー成形を同時に行う、射出ダイレクトブロー成形品用の金型設計・製作を強みとしております。
まずは製品事例を一度ご覧ください。
03
強度や精度を向上させるための分割面の最適化もお任せください!
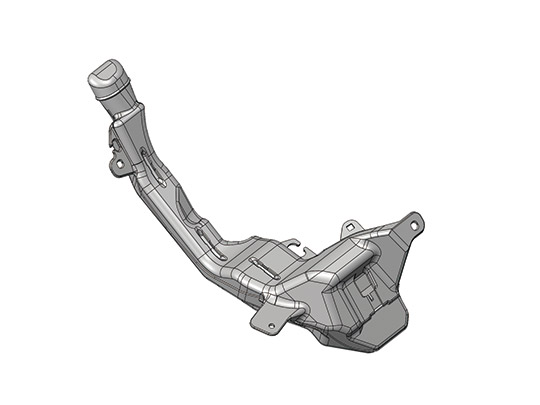
当社のダイレクトブロー金型は、ただ成形品を形にすることだけを目的にせずに、成形品の強度や精度を向上させる提案も行っています。
例えば、形状的に樹脂が膨らみづらい部分には適切なパーティングの分割面を設定したり、溶着リブと呼ばれる構造で割れや剥がれが起きない仕様にする、といったご提案を行っております。
ただ、部品を一体化するだけでなく、成形品の用途や課題を踏まえた上で、最適な金型構造のご提案をいたします。
Service 特殊ブロー金型による部品一体化提案 事例
-
ドローンタンク(薬剤散布) 金型
- 種類 : ダイレクトブロー成形品
- 業界 : 農業機具
-
薬剤散布用背負いタンク(プレス形状・タンク形状を一体成形) 金型
- 種類 : ダイレクトブロー成形品
- 業界 : 農業機具
-
2連ダクト(トラック向け) 金型
- 種類 : 3次元ブロー成形品
- 業界 : トラック
-
”インサート部品9個を配置”ダクト 金型
- 種類 : ダイレクトブロー成形品
- 業界 : トラック
-
自動車向け 複雑形状パイプ 用金型
- 種類 : 3次元ブロー成形品
- 業界 : 自動車
-
トラック向け 吸気バーチカルダクト 金型
- 種類 : ダイレクトブロー成形品
- 業界 : トラック
-
トラック向け 長尺ダクト 金型
- 種類 : 3次元ブロー成形品
- 業界 : トラック
-
海外自動車向け パイプ 用金型
- 種類 : 3次元ブロー成形品
- 業界 : 自動車
-
海外生産”インサート部品5個を配置”パイプ 金型
- 種類 : 3次元ブロー成形品
- 業界 : 自動車
-
S字ダクト 用金型
- 種類 : 3次元ブロー成形品
- 業界 : 自動車
-
小型”インサート部品を4個を配置”ダクト 金型
- 種類 : 3次元ブロー成形品
- 業界 : 自動車
-
建機向け ダクト 用金型
- 種類 : 3次元ブロー成形品
- 業界 : 建機
-
吸気バーチカルダクト 金型
- 種類 : ダイレクトブロー成形品
- 業界 : トラック
-
自動車向け ダクト 用金型
- 種類 : 3次元ブロー成形品
- 業界 : 自動車
Column 特殊ブロー金型による部品一体化提案に関連するコラム
-
2023/09/22
ブロー成形
ブロー成形の代表的な3つの成形方法
一言でブロー成形といっても、成形する製品の形状等によってその成形方法は異なります。今回のコラムではブロー成形の種類についてご説明させていただきます。… -
2023/09/22
3次元ブロー成形
ブロー成形の概念を変える!3次元ブロー成形とは?
3次元ブロー成形を行うための3次元ブロー金型は、高度な技術とノウハウが求められるため、熟練した職人による製作が重要です。金型の設計や製造、運用において、経験豊富な専門家たちが必要とされる金型です。今回は… -
2023/09/22
ブロー成形
射出成形とブロー成形の違いを徹底解説
今回のコラムでは射出成形とブロー成形の違いについてご説明させていただきます。
まずは上記2つの違いをご説明させていただく前に、双方ともプラスチック成形の… -
2023/09/22
ブロー成形
ブロー成形品” タンク ”
-
2023/09/22
ブロー成形
射出成形じゃなくなぜブロー成形?その驚愕の理由とは
なぜブロー成形を選ぶのか。
射出成形が主流な中、ブロー成形を選択した製品とその理由を説明します。…
Faq 特殊ブロー金型による部品一体化提案に関連するQ&A
-
-
Q.ブロー成形と射出成形の違いはなんですか?
-
A.違いを、1つのポリタンクから例えると、タンクがブロー成形、注入口のキャップ蓋が射出成形です。
射出成形は、重ねた金型の隙間(成形品となる部分またはキャビティ内)に溶かして液化した樹脂を高い圧力で注射のように注入し、冷却固化させる成形方法です。凸凹の隙間に樹脂を圧入するので、その隙間が製品の肉厚になります。ブロー成形よりも複雑な3D 設計を可能にしており高精度ではある一方、それに伴いブロー成形よりも製作工期と、製作コストが高くなる傾向にあります。よってコスト面から、一般的に小ロット生産には向いておりません。違いを、1つのポリタンクから例えると、タンクがブロー成形、注入口のキャップ蓋が射出成形です。一般的にインジェクション成形とも呼ばれています。インジェクションブロー成形(射出+圧入)とは意味合いが違います。
-
Q.ブロー成形で試作用の金型を作りたいのですが可能ですか?
-
A.はい。製品の成立性・低価格・短納期をご提案します。
もちろん試作型から量産化への転用を前提とした金型製作も可能です。
-
Q.ブロー成形のメリットはなんですか?
-
A.下記、一般的なメリットを5つお伝えします。
① 金型製作コストが安価:
射出金型より構造がシンプルで、部品点数も少なくできるため費用を抑えられることに加えて、製作工期も短くなります。
金型製作においては製品開発における試作型や、小ロット生産にコスト面で適しています。② 形状変更や修理の容易性:
射出金型に比べて金型の構造がシンプルなことで、構造上の複雑性および制約が少ないため、形状の改造に向けた構成が比較的に容易です。③ 高い生産効率:
比較的に成形プロセスがシンプルで、射出成形よりリードタイムが短いです。
継続的に製品を量産成形できるので大量生産に向いております。④ 一体化成形:
食用油の容器のように”持ち手”などの異形を一体化成形できます。
また具体例としてクリップやブラケットなどの射出成形品や、金属性ナットをインサートして成形することも可能です。⑤ 多層成形ができる:
異なる樹脂材料を積層させて多層化したパリソンを生成します。
各種樹脂の特性を利用して、光沢性・耐薬品性・ガスバリア性(酸素)など多層構造の製品を可能にします。
例えば、食用油・調味料(ソース・マヨネーズ)・化粧品の容器類です。
-
Q.ブロー成形のデメリットはなんですか?
-
A.下記、一般的なデメリットを3点お伝えします。
① 肉厚の制御が難しい:
パイプ状に落ちてくるパリソン(溶融樹脂)を金型の2面(製品形状面)で挟み込み、パリソンの内部から膨らますと、パリソンの外面は金型に密着し、冷却固化をしはじめ製品の外観面を成形します。その反面、パリソンの内面は空気圧力がかかるだけで金型に接触しません。パリソンの外面と内面で温度差が生じており冷却固化のバラつきと、製品デザインにも左右され肉厚が不均一となる。
加えて、パリソンは溶融樹脂なので、上方から下方に自重で垂れていく”ドローダウン”を生じて”偏肉”になりやすいです。
しかし、偏肉の防止や肉厚をコントロールをするために、成形機の樹脂吐出口(ヘッド)の調整や樹脂の粘度、空気圧の調整など成形条件の最適化と、吹き込みや型締めのタイミングを計る成形技術により対策されています。はめ合わせが必要なパイプ形状の製品などは、後加工により内径切削を施します。➁ バリの発生と処理:
金型から離型した成形品には、上方・下方にパリソンを挟んだ余剰部分となるバリが残ります。外観の良さや、手に触れる部分はバリの処理が必要です。要求される品質によって仕上げ加工の程度は異なります。イメージとしては、マヨネーズ類の容器底面の中央にある線状の筋です。また、製品形状の幅よりも大きいパリソンを金型全面で挟む”総バリ”設計もあり、成形品外周の大きなバリを取らなくてはなりません。取り除いたバリは成形で再利用されます。③ 複雑な形状が苦手:
風船が円の中心から膨らむイメージで、パイプ状のパリソンが製品面に密着していくため、製品デザインとして、丸みが小さい・エッジが多い・谷状の狭い形状等は苦手です。冷却固化の影響も合わさり、樹脂のまわりが悪くなることで薄肉やパンクなどのリスクがあります。設計段階で技術者の知見が必要となります。
-
Q.ブロー成形の成形不良にはどのようなものが挙げられますか?
-
A.ブロー成形は溶融樹脂を垂らして成形するため、製品デザインや金型の設計が要因して様々な事象がありえます。簡潔に代表的な実例を説明します。
① 偏肉:
製品の特定部分の肉厚が不均一(厚薄)となること。製品デザイン、金型設計、成形条件が不適切な場合に発生します。
ダイレクトブロー成形は、溶融樹脂(パリソン)が自重で重力方向に垂れ下がる”ドローダウン”により上方と下方で偏肉(下方が厚い)が生じます。対策として成形温度や材料選定など成形条件の最適化と、偏肉を考慮または利用した設計が重要です。➁ 薄肉:
パリソンを膨らます際に、製品の特定部分の肉厚が薄くなり、強度や耐久性に影響がでること。口径よりも底の深いグラスコップをイメージしてください。そのグラスの中で飲み口側から風船を膨らますと、狭い口元から密着して徐々に深さ方向へ密着しながら伸びて膨らんでいきます。これを金型に置き換えて、飲み口が金型のPLとして(分割した金型の接合面)、風船をパリソンとします。徐々に密着しながらパリソンは冷めて固くなることで樹脂の伸延性は低くなります。最終的に底部分に到達した樹脂の肉厚はPL側より薄くなります。対策は、成立性と補強を加味した製品デザインや金型設計と成形条件の最適化により薄肉を防ぎます。③ ピンチオフ(喰い切り)の駄肉:
ブロー成形は、金型の製品デザインを2面に分割させ、PL(分割の境界線)同士を重ね合わせて成形します。このPL部分にパリソンを挟んだ場合、樹脂の折れ込みによって盛り上がり、製品内部のPL部分に肉だまり(膨らみ)が発生することがあります。例えばPLで2分割されたφ100の開口部を成形します。後にφ99.9のパイプを差し込むと、開口部の内径に発生した肉だまりが邪魔をして差し込めない不良が起こりえます。
要求仕様にもよりますが、はめ合わせが必要な製品は、内径切削の後加工が必要です。また、製品のピンチオフ形状(喰い切り部)の工夫で、後加工の手間を省いた手法もございます。④ ピンチオフの窪み(ヒケ):
金型が閉じるとき、パイプ状のパリソン(溶融樹脂)がPL面に接触する部分に押し潰されて融合(ウェルド)します。次に膨らましますが、パリソン内側の押し潰されたPL部分は挟まれて絞られた状態から膨らむので、PLに沿った線上の窪みが残ります。(樹脂のヒケも関係する)製品外観面に影響はありませんが、この製品内部(PL部分)の窪みが製品の脆性に悪影響を与えるかもしれません。
しかし、金型設計でピンチオフ形状の工夫をすれば対策は可能です。⑤ パンク:
成形中に製品の特定部分が破れることです。吹き込みによる膨張空気圧が高すぎたり、偏肉または薄肉、過剰な冷却、素材の不適合などからパンクが生じます。また型締めの際に、山形のエッジ形状がパリソンを挟み切ってしまうケースもあります。
-
Q.ブロー成形品に他の部品を付けることはできますか?
-
A.はい。金型内の製品形状にプラスチック部品(射出成型品)や金属製ナットをセットして、一体化成形できる金型を設計します。
なかには、製品の内部(空洞)にプラスチック部品をセットをして成形できる金型を製作した実績もございます。ウレタンなどの貼付けは後施工となります。
-
Q.ブロー製品とはどのようなものがありますか?
-
A.空調ダクト、PETボトル、容器類、アミューズメントのオブジェなど、中身が空洞となる構造のものが対象になります。
ブロー製品の特徴は中身が空洞となる構造と言えます。自動車のガソリンタンク・スポイラー・空調ダクト、アーケードゲーム機のイス、看板、バリケード、PETボトル、容器類、アミューズメントのオブジェなど、日常的に目にする物や建機、農機とさまざまな製品があげられます。
-
Q.ダイレクトブローと3次元ブローの違いはなんですか?
-
A.成形方法として、ダイレクトブローはタンクや容器類、3次元ブローは湾曲するパイプまたはホース形状の製品と一般的に分けられます。
比較例として、3次元ブロー成形の利点をあげて説明します。
まず両方の金型で”S字形状のパイプ製品”を成形するとします。
ダイレクトブロー成形はパリソンを縦(天地)に垂らすので、自重で樹脂が下方に垂れるドローダウンが発生し、上方と下方で製品断面の肉厚が不均一となります。直線的にしかパリソンを押し出せないので、製品幅が広いと、パリソンを金型で挟む面積が必然的に大きくなり、製品外周に多くのバリが付いて残ります。一方、3次元ブロー成形では金型は横置きとなり、コンピュータ制御にてパリソンを湾曲形状に沿って寝かすように配置できます。金型でパリソンを挟むのは両端のピンチオフ(喰い切り)のみなので、大部分のバリとドローダウンの発生を回避し、バリ部の仕上工程やロス材の低減となります。
大部分の樹脂を噛まないことで、製品外観面と寸法精度も良くなります。よって、S字形状のパイプ成形においては3次元ブロー成形が生産性と品質においても、有効的と言えます。
また、パリソンを誘導できる利点から樹脂材料を交互に切り替えて硬質部分と軟質部分を一体で成形することができます。自動車など狭い場所への格納を目的とした、複雑に湾曲したホース形状は3次元ブロー成形が適しています。
-
Q.ダイレクトブロー成形(押出ブロー成形)とはどのような成形方法ですか?
-
A.樹脂を金型の形状面に密着させて、水冷や空冷といった冷却工程で硬化させる成形方法です。
押出成形機のヒーターで原料を溶かし、シリンダーに格納したスクリューによって練りこみながら、末端のダイス(吐出口)へ押出します。
開いた金型の間に、肉厚が一定となるようにしたパイプ状の溶融樹脂を縦方向(天地方向)へ直線的に垂らします。
(溶融樹脂は”パリソン”と呼ばれます)その加熱されたパリソンが冷めて硬化しないうちに、開いていた金型を閉じて、パリソン内の空洞にブローピン(吹き込み)を刺しこみ空気を圧入して風船のように膨らまします。膨らむと同時に残留した空気と樹脂から発生するガスをベントを通じて金型外へ排気します。
そして樹脂を金型の形状面に密着させて、水冷や空冷といった冷却工程で硬化させる成形方法です。
離形後、余剰分のバリの除去、穴あけなどの仕上げ加工を施します。また大きい物を成形するときは、製品形状の幅よりも幅広いパリソンを必要とするので、バリの余剰分が多く残る”総バリ設計”となります。
複数の押出機を利用した多層成形も可能です。
-
Q.3次元ブロー成形とはどのような成形方法ですか?
-
A.ダイレクトブロー成形の成形プロセスを応用した方法です。
ダイレクトブロー成形では、合掌するように縦方向の金型が開閉しますが、3次元ブロー成形では金型を寝かした横置きの設置となり、上型と下型の構造となります。この下型へ、コンピュータ制御によりダイス(パリソンを押し出す吐出口)が湾曲部や複雑なキャビティ形状に沿って誘導され、パイプ状のパリソンを寝かすようにセットしてから切り離します。 セット後、上型を閉じてパリソンの両端をピンチオフ(喰い切り)で挟み、その端面に吹き込み針(ブローピン)を刺しこみ空気を圧入して成形します。離型後、バリの除去、穴あけなどの仕上げ加工を施します。 多層成形が可能で、3次元多層ブロー成形とも呼ばれています。
-
Q.ブロー成形品の樹脂材料で、過去にどのような実績がありますか?
-
A.下記、過去の実績一例です。
熱可塑性樹脂となり、
ナイロン(PA), ポリプロピレン(PP), ポリカーボネート(PC), ポリエチレン(PE), 高密度ポリエチレン(HDPE),エラストマー(TPO・TPA 他) , エバール(EVOH)など多岐にわたります。またエンプラなどの材質も、一度ご相談ください。
-